- Home
- Used Equipment
- Equipment Packages
- Small Tractors
- All Product Lines
- Departments
- Company Profile
- Parts Online
- Contact Us
- John Deere Specials - Save Some Green
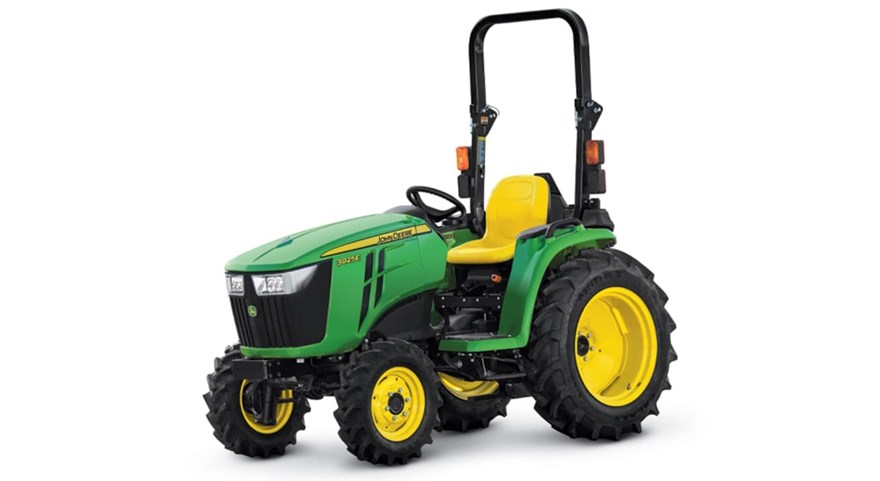
3025E
Compact Utility Tractor
- Standard four-wheel drive (4WD) for maximum traction
- Tightest turning radius in its horsepower class
- Hydro transmission with Twin Touch™ pedals for ease of use
For pricing and additional discounts, see your local John Deere Dealer.
- Buy Online
-
Get a Quote
Get A Quote
Fields with asterisks* are required. Please email our helpful staff with any questions or comments using the contact form.
-
Send to a Friend
Send To A Friend
Fields with asterisks* are required. Your friend will receive an email that contains a reference to this page. Please send this email only to people you know who would be interested in this information.
-
Payment Calculator
Loan Calculator
Use the Loan Calculator to help you determine the financing and payment options that are best for you.
**The accuracy of this calculator and its applicability to your circumstances is not guaranteed. You should obtain personal advice from qualified professionals. This information is provided for illustrative purposes only and does not constitute an application. This notice does not guarantee loan approval, nor is it an offer or commitment to make a loan to you on the above terms.
- View Product Brochure
- View Implements & Attachments Brochure
-
Share
Features
Powerful, diesel engine delivers plenty of power under heavy loads

3025E
The 1.642-L (100.2 cu in.) displacement, liquid-cooled 3TNV88F-EPJT1 Yanmar® diesel engine provides 18. kW (24.4 hp) to the 3025E.
Model |
Number of |
Engine |
Rated rpm |
Gross engine hp* |
Gross engine ps* |
PTO hp |
3025E |
3 |
1.642 L (100.2 cu in.) |
2400 |
18.2 kW (24.4 hp) |
24.7 |
13 kW (17.4 hp) |
*Engine kW (hp), gross SAE J1995: 18.2 (24.4) at 2400 rpm, PS
Displacement, L (cu in.): 1.642 (100.2)
3032E
The 1.642-L (100.2 cu in.) displacement, liquid-cooled 3TNV88C-NJT Yanmar diesel engine provides 22.9 kW (30.7 hp) to the 3032E.
Model |
Number of |
Engine |
Rated rpm |
Gross engine hp* |
Gross engine ps* |
PTO hp |
3032E |
3 |
1.642 L (100.2 cu in.) |
2500 |
22.9 kW (30.7 hp) |
31.2 |
18.6 kW (25 hp) |
*Engine kW (hp), gross SAE J1995: 22.9 (30.7) at 2500 rpm, PS
Displacement, L (cu in): 1.642 (100.2)
3038E
The 1.568-L (95.68 cu in.) displacement, turbocharged, liquid-cooled 3TNV86T-NJT Yanmar diesel engine provides 27.4 kW (36.7 hp) to the 3038E.
Model |
Number of |
Engine |
Rated rpm |
Gross engine hp* |
Gross engine ps* |
PTO hp |
3038E |
3 |
1.568 L (95.68 cu in.) |
2500 |
27.4 kW (36.7 hp) |
37.2 |
22.4 kW (30 hp) |
*Engine kW (hp), gross SAE J1995: 27.4 (36.7) at 2500 rpm, PS
Displacement, L (cu in.): 1.568 (95.68)
The engine uses the latest technologies to optimize fuel economy, improve control and accuracy, and reduce environmental impact. The common rail system (CRS) optimizes fuel economy and reduces operating costs comparted to engines not using CRS technology. High-pressure injection atomizes fuel into finer particles which burn more completely. It results in improved fuel economy and a lower cost of operation.
The electronic control unit (ECU) provides optimum fuel control and accuracy. ECU monitors and controls the engine. It continuously monitors engine conditions and adjusts the fuel delivery accordingly to ensure optimum performance and emissions.
The engine comes with an after-treatment system. The system operates automatically. The exhaust filter consists of a diesel particulate filter (DPF) which captures particulate matter (PM) contained in the exhaust gas. Using a natural cleaning process, most of the PM trapped in the exhaust filter is eliminated by the heat of the exhaust stream generated by normal use. In situations of low temperature, engine speed, or load factor, an active cleaning cycle is initiated. In this cleaning cycle, the exhaust gas temperature is raised by injecting additional fuel during the exhaust stroke of normal vehicle operation to the diesel oxidation catalyst (DOC).
After many hours of use, the exhaust filter may require an ash removal service.
DPF cleaning
Depending on the load that the tractor is under, as well as ambient temperature, humidity, and engine speed, the DPF may build up with particulate matter, thus requiring cleaning. Filter cleaning is determined by one of three factors:
- A prescribed time-based estimation of needed filter cleaning
- DOC/DPF pressure sensors
- A particulate matter buildup estimation based on load conditions
Once one of the three conditions has been met, filter cleaning will occur.
There are three different types of filter cleaning processes:
- Passive filter cleaning
- Active filter cleaning
- Parked filter cleaning
Passive filter cleaning
Passive filter cleaning occurs naturally when the engine is generating enough heat to oxidize particulate matter. This automatic process occurs continuously during normal operating conditions. No tractor icons or symbols appear on the display during passive filter cleaning.
NOTE: Passive filter cleaning requires no operator involvement, and there is no interruption to tractor operation.
Active filter cleaning
If conditions (temperature, load, or speed) for passive filter cleaning cannot be achieved, then PM is removed using active filter cleaner.
To achieve the required conditions, exhaust temperature management (ETM) manages the initiation and duration of active filter cleaning. ETM can adjust numerous engine parameters and/or inject a small quantity of fuel into the exhaust stream for a short duration. The fuel turns to vapor and chemically reacts with the catalysts in the DOC to create heat to oxidize the PM.
It is important to note that at no time is the fuel in the DOC/DPF ignited, and there is no flame within the DOC/DPF.
Like passive filter cleaning, active filter cleaning requires no operator involvement, and there is no interruption to tractor operation.
Parked filter cleaning
In some instances where passive and active filter cleaning have not fully cleaned the PM from the system, a parked filter cleaning may need to take place. In general, the only time a parked filter cleaning will need to occur is when automatic filter cleaning has been disabled for an extended period of time and multiple warnings to engage filter cleaning were ignored or if the tractor has been used during light load conditions. Additionally, when the automatic filter cleaning process has been deliberately interrupted multiple times, or if active filter cleaning has failed numerous times due to a failed component, a parked filter cleaning may be requested. In these rare instances the operator will have to park the tractor and start the filter cleaning process.
The parked filter cleaning process needs to be activated based on usage and operation of the tractor. The process will take approximately 30 minutes. See the operator's manual for more details.
This system constantly monitors the soot level of the tractor; making sure the tractor is always in peak performance condition. This ensures high performance at all times.
NOTE: Number of hours since last regeneration and soot level percentage are viewable on LCD display.
Key features of the engine are:
- Economical cast-in-block cylinder design for good cooling and long life
- Direct fuel injection
- Improves starting
- Injects fuel directly on top of pistons for more efficient combustion
- Develops more horsepower per liter (gallon) of fuel than indirect injection engines
- Aluminum alloy pistons are lightweight to reduce connecting rod bearing loads and provide good heat transfer characteristics
- Design permits tighter tolerances and neutralizes expansion of the piston, which reduces blow-by and noise from piston slap
- Top rings are higher on the piston and a thinner head gasket is used to greatly reduce the volume of unburned waste gases and increase combustion efficiency
- Timing gears and injector drive gears have a helical profile to reduce engine noise
- Auto-bleed fuel system
- There is no need to prime the system if the tractor runs out of fuel
- The system will self-prime the injection pump, lines, and injectors, providing fast fuel recovery for easier starting
- High-capacity lubrication system provides filtered oil, under pressure, to all engine bearings for long life
- Key start and shutoff eliminate fuel shutoff knob
- Electric solenoid shuts the fuel supply off immediately when key is turned off, which replaces the need to pull a fuel shutoff lever like many older tractors
- Fuel filter with replaceable element
- Water separator with additional replaceable filter element
- See-through coolant recovery tank permits operator to check coolant level without removing radiator cap
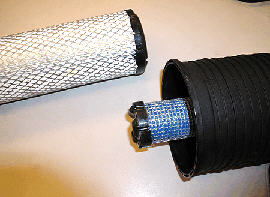
- Dry-type air cleaner with safety element
- Dual element design for added engine protection
- Easy to service
- Hood can be easily opened without tools for full access to the engine
- Easy access to engine check and fill points on the right-hand side of the tractor by removing the side panels.
Yanmar is a trademark of Yanmar Company Limited.
Easy-to-use hydrostatic transmission (HST) increases tractor performance
The 3E Tractors are available with a two-range hydrostatic transmission (HST) incorporated in a die-cast aluminum transmission case. Fluid under pressure transmits engine power to the drive wheels via a closed-loop pump and motor arrangement. Infinite ground speeds allow the operator to match the speed of the tractor to the job.
- No clutching for fast and easy direction changes
- Twin Touch™ foot pedals for quick and easy forward/reverse operation
- Transmission oil cooler cools transmission oil for longer transmission life
Safety features of the HST include:
-
The tractor will only start with the range lever in neutral
-
The engine will shut off if the operator leaves the seat unless the range lever is in neutral
-
The engine will shut off if the operator leaves the seat and the power take-off (PTO) is engaged
Twin Touch foot controls
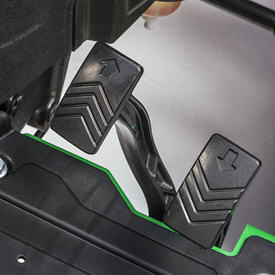
Key John Deere advantage - John Deere's Twin Touch foot controls offer several key advantages over competitive HST models tractors.
-
Some competitive hydrostatic tractors use a treadle pedal (toe-heel) design foot control for operation of the HST
- Requires the operator to use both toe and heel to change direction, resulting in increased operator fatigue
- The Twin Touch configuration also makes it easier to "inch" the tractor forward or rearward (i.e., when attaching to implements)
Optional cruise control
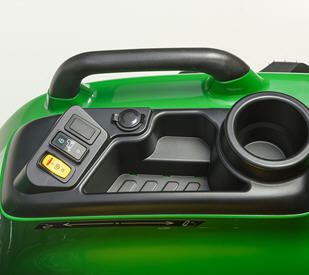
The 3E Series Tractors can be outfitted with an optional cruise control switch that is installed on the right-hand control console. This gives operators the ability to keep a constant speed when in transportation, field mowing, or other applications where extended use of the transmission is needed. This kit is very quick and easy to install for those who desire this feature.
Integrated hydrostatic pump and motor
- Sauer-Danfoss® company provides the integrated pump and motor; this assures that the components are matched to each other, providing maximum efficiency
- Reduces powertrain shock loads
- Provides strength and durability needed for operating such attachments as loaders
- One reservoir (with one check point and fill point) for the transmission, differential, and hydraulic system speeds up daily maintenance
- Mechanically actuated by Twin Touch foot pedals allow selecting both directions of travel and speed with the touch of a toe
Transmission reservoir fluid checkpoint
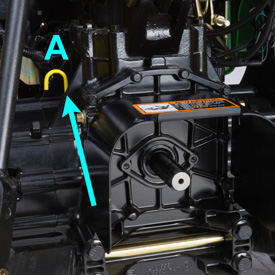
- Easy-to-reach transmission fluid dipstick allows for frequent checks of the transmission fluid level.
Transmission fill point
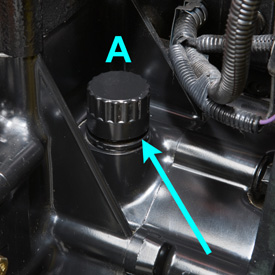
- Easy-to-reach transmission fill point (A) is located on top of rear axles on the right-hand side.
Integrated brake and differential lock pedal
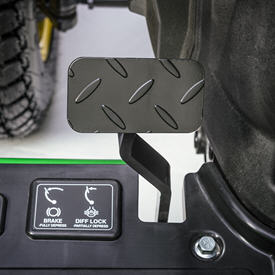
- Foot-actuated differential lock is integrated into the brake pedal to simplify operator controls; the differential lock is included as base equipment to assist traction in tough spots.
- Press the brake pedal down half way to engage the differential lock that locks the rear axle for improved traction in tough spots.
Sauer-Danfoss is a trademark of Sauer-Danfoss Incorporated.
Clean and simple operator station is comfortable and convenient
![Clean and simple operator's station (shown with optional selective control valve [SCV] levers)](https://salesmanual.deere.com/sales/salesmanual/images/NA/tractors/cuts/3_series/r4d098800_operator_station.jpg)
An uncluttered design gives operators of all sizes plenty of room to be comfortable. Color-coded controls are located on either side of the operator.
- The hydrostatic transmission (HST) and brake pedals are designed and located for maximum comfort and ease of use.
-
Contoured, comfortable seat enhances operator comfort.
- Seat position adjusts fore and aft.
- Seat flips forward for protection from the elements.
- Flat operator platform provides for easy entry to and exit from the tractor.
-
Folding Roll-Gard™ rollover protective structure (ROPS) and retractable seat belt increase operator safety.
Operator presence system:
-
If the operator leaves the seat when the tractor is in gear, the engine shuts down
-
If the operator leaves the seat when the power take-off (PTO) is engaged, the engine shuts down
Left-side step
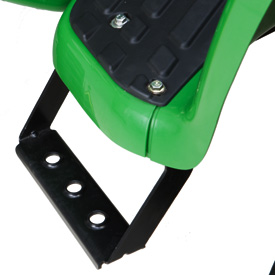
-
The left-side step allows for easy access on and off the tractor.
-
Foot platform has a non-skid surface for sure footing.
Seat
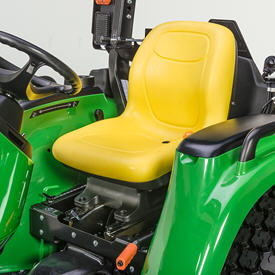
The thick, soft padding on this seat provides a smooth and comfortable ride.
- Seat flips forward for protection from the elements.
- Adjustable using the fore and aft lever located under the seat, the seat slides on ramped rails to provide comfortable access to all controls.
Instrumentation
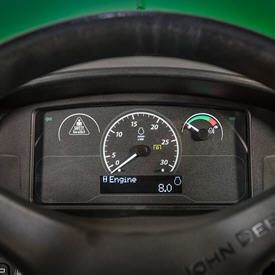
Easy-to-read instrument panel includes the following:
- Tachometer
- Low oil pressure indicator light
- Battery discharge indicator light
- PTO engagement indicator light
- Signal/hazard lamp indicator lights
- Multifunction liquid crystal display (LCD) display (hours, filter cleaning information, etc.)
- Filter cleaning status indicator light
Fuel gauge
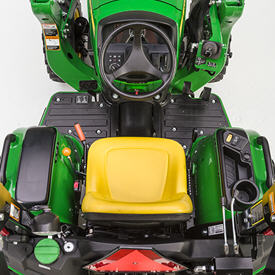
All 3E Series Tractors come standard with a fuel gauge that is easy to read from the operator's station to ensure operators do not run out of fuel.
Safety
Operator presence switch (OPS) in seat:
-
OPS requires the operator to be in the seat to operate the transmission or PTO.
-
ROPS is designed to meet or exceed American Society of Agricultural and Biological Engineers (ASABE) safety standards.
-
Reflective ROPS strips for better tractor visibility.
-
Seat belts are in base equipment on all John Deere compact utility tractors.
-
Key switch interlock prevents bypass starting.
-
Visual PTO warning light on the instrument panel alerts the operator when the PTO is running.
-
Turn signal and flashing warning lights operate according to ASABE standards.
-
Slow-moving vehicle (SMV) sign is provided for road transport.
Park brake
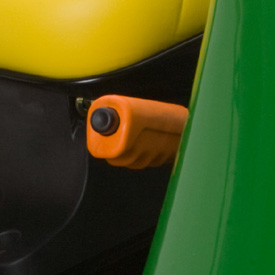
-
Automotive hand-style park brake for easy on/off.
-
Instrument panel has an indicator light for the park brake.
Two-post Roll-Gard ROPS
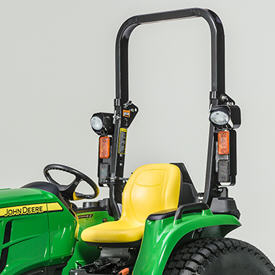
3E Series Tractors are equipped with Roll-Gard ROPS. These folding ROPS meet the ASABE standards for compact utility tractors.
- With the Roll-Gard ROPS folded down, producers can easily to get their tractor into a garage with a standard 2.1-m (7-ft) garage door.
NOTE: The use of seat belts is recommended at all times when operating the 3E Series Tractor with the folding ROPS upright.
An optional canopy (LVB25334) is available to help protect the operator from the elements.
Optional two-spool rear selective control valve (SCV) for superior implement performance
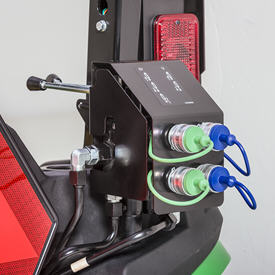
3E Series Tractors can be equipped with a field-installed rear hydraulic remote kit, providing two additional hydraulic spools on the back of the tractor. This kit can be field installed on a tractor with a loader or without a loader.
NOTE: Not compatible with the power beyond kit.
The functions are completely separate from the loader. These rear remotes can be hooked up to a wide variety of implements and attachments such as follows:
- Hydraulically angled blade
- Hydraulically controlled chute/spout on a 3-point hitch-mounted snow blower
- Hydraulic scarifiers on a box blade
- Many other hydraulic rear attachments
This versatile kit gives 3E Series Tractor operators the options they desire for putting their tractors into a wide range of tasks.
The first spool is equipped with a float position, giving the operator the ability to contour the landscape and improve the final grade with certain implements.
NOTE: Neither of the spools in this kit are equipped with a detent position; therefore, they should not be hooked up to anything with a motor, as the valve was not designed to be run open. The kit is designed for momentary, on-demand hydraulic flow such as moving a cylinder.
Optional iMatch™ Quick-Hitch feature allows for easy implement hookup
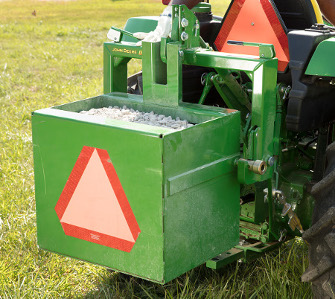
One of the greatest operator concerns involves difficulty in attaching tractor implements. John Deere has addressed this issue with the iMatch Quick-Hitch.
The iMatch Quick-Hitch provides easy hookup and a guaranteed fit for all Category 1 implements that are designed to meet the American Society of Agricultural and Biological Engineers (ASABE) Category 1 Standard S278.6 for quick-attach hitches.
- All implements require a set of bushings in order for the attachment to fit and work properly with the iMatch Quick-Hitch. One set of bushings comes with the iMatch Quick-Hitch.
NOTE: The bushing set can be seen in the picture above. These bushings allow the hooks on the iMatch and the pins on the implement to fit together properly. All other implements (box blades, tillers, rear blades, etc.) will require a set of bushings to enlarge the pin to fit with the iMatch hooks. Bushings of different lengths can be found in the parts system or through a bushing supplier (see dimensions below).
- Upper bushing
- Inside diameter: 1.93-1.95 cm (0.76-0.77 in.)
- Outside diameter: 3.15-3.18 cm (1.24-1.25 in.)
- Lower bushings
- Inside diameter: 2.24-2.26 cm (0.88 to 0.89 in.)
- Outside diameter: 3.63-3.66 cm (1.43 to 1.44 in.)
Excellent serviceability reduces operational costs and improves productivity
Regular service and maintenance are essential to the performance, productivity, and longevity of the tractor.
- Easy access to most regular service points minimizes service time.
- Four quarter turn fasteners allow operators to easily remove the engine side panels without tools to access the engine compartment.

- Tractors are equipped with extensive onboard self-diagnostic capabilities and are fully compatible with the John Deere exclusive Service ADVISOR™ system.
- Hydraulic oil service interval increased to 1200 hours when using Hy-Gard™ products.
- Hydraulic oil filter will need to be changed every 400 hours.
- Fuel tank is located on the rear of the tractor to allow for easy access when fueling.
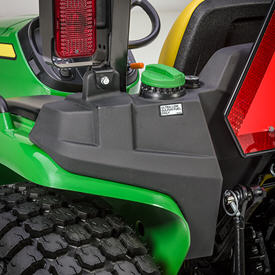
- Gas-lift hood support eliminates the need for a mechanical prop rod.
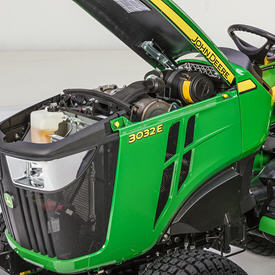
- Daily service requirements are minimal and simple to accomplish. Most service interval requirements can be performed with a basic understanding of procedures and common tools.
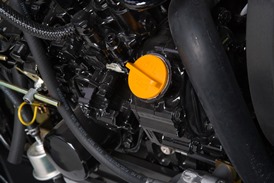
All items in the daily service schedule can be performed without the use of tools:
- Engine oil, hydraulic oil, coolant level, and the water separator can be conveniently accessed.
- The engine can be easily accessed by simply raising the hood for more periodic maintenance checks.
NOTE: Always refer to the operator’s manual for complete maintenance and service recommendations.
Key Specs
Engine power (gross) | SAE J1995 rated power: 18.2 kW 24.4 hp 24.7 PS at 2400 rpm |
---|---|
Power take-off (PTO) power | 13 kW 17.4 hp |
Steering hydraulics | 15 L/min 4 gpm |
Implement hydraulics | 20.2 L/min 5.3 gpm |
Hitch type | Category 1 |
Lift capacity, 24-in. behind link arms | 615 kg 1356 lb |
Standard transmission; forward/reverse | Hydrostatic transmission (HST) |
Cruise control | Optional |
Approximate shipping weight (open-station; cab) | Open operator station (OOS): 1181 kg 2603 lb Cab: Not applicable |
Wheelbase | 1593 mm 62.7 in. |
Engine
Family | EYDXL1.64NDA FYDXL1.64NDA GYDXL1.64NDA |
---|---|
Manufacturer | Yanmar |
Engine model | 3TNV88F-EPJT2 |
Engine power (gross) | SAE J1995 rated power: 18.2 kW 24.4 hp 24.7 PS at 2400 rpm |
Power take-off (PTO) power | 13 kW 17.4 hp |
Rated engine speed | 2400 rpm |
Type | Diesel |
Injection pump type | Direct injection |
Aspiration | Natural |
Emissions compliance | Final Tier 4 |
Cylinders/displacement | 3 / 1.64 L 3 / 100.2 cu in. |
Number of cylinders | Three |
Cylinder liners | Cast-in-block |
Bore and stroke | 88 x 90 mm 3.46 x 3.54 in. |
Compression ratio | 19.1:1 |
Lubrication | Pressurized |
Cooling system | Water pump |
Air cleaner | Dual element |
Engine torque at rated speed | 72.4 Nm 53.4 lb-ft |
Fuel tank capacity | 28.5 L 7.5 U.S. gal. |
Electrical
Battery size | 500 CCA |
---|---|
Alternator (12-V) | 55 amp |
Starter size | 1.4 kW 1.9 hp |
Fuel system
Type | Direct injection |
---|---|
Fuel consumption |
Transmission
Standard transmission; forward/reverse | Hydrostatic transmission (HST) |
---|---|
Optional transmission; forward/reverse | |
Left-hand reverser | No |
Transmission gear ranges | |
Final drive | Spur gear |
Brakes | Wet disk |
Steering | Power steering |
Clutch, wet/dry | |
Clutch disk diameter wet clutch | |
Axle capacity | Front 880 kg 1940 lb Rear 1200 kg 2645 lb |
Creeper | No |
Cruise control | Optional |
Differential lock | Yes |
Drawbar maximum vertical load |
Hydraulics
Type | Open center |
---|---|
Pump rated output | Steering 15 L/min 4 gpm Implement 20.2 L/min 5.3 gpm 35.2 L/min 9.3 gpm |
Pump type | Dual gear |
Maximum operating pressure | 172 bar 2495 psi |
Draft control sensing | Position control |
Remote control valves available | Up to two (optional) |
3-point hitch
Type | Category 1 |
---|---|
Lift capacity, 24-in. behind link arms | 615 kg 1356 lb |
Power take-off (PTO)
Standard | Rear - 540 rpm |
---|---|
Optional | |
Control | Independent |
Clutch | Wet disk |
Brake (for mid and rear PTO) | Wet disk |
Engagement method |
Fluid capacities
Crankcase with filter | 4.5 L 4.8 gal. |
---|---|
Transmission and hydraulic system | 20.8 L 22 qt |
Final drive
Type | Spur gear |
---|---|
Differential lock |
Operator station
Rollover protective structure | Type Foldable |
---|---|
Platform - flat/straddle | Straddle |
Gear shift location - console/floor | Left-hand side |
Cab
Compliance | |
---|---|
Visibility | |
Air conditioning, temperature differential | |
Doors | |
Noise rating | |
Seat equipment |
Dimensions
Height | |
---|---|
Wheelbase | 1593 mm 62.7 in. |
Front axle clearance | Minimum: 299 mm 11.8 in. Maximum: 333 mm 13.1 in. |
Turning radius with brakes | |
Turning radius without brakes | 2.9 m 9.4 ft |
Limited slip differential | |
Approximate shipping weight (open-station; cab) | OOS: 1181 kg 2603 lb Cab: Not applicable |
Tires
Front | R1 Bar: 7-14 R3 Turf: 27x8.5-15 R4 Industrial: 25x8.5-14 R4 Industrial: 27x8.5-15 |
---|---|
Rear | R1 Bar: 11.2-24 R3 Turf: 41x14-20 R4 Industrial: 15-19.5 R4 Industrial: 43x16-20 |
Front tread range | |
Rear tread spacing |
Miscellaneous
Toolbox | |
---|---|
Tilt steering wheel | |
12-V Outlet |
Additional information
Date collected |
---|
Central Jersey Equipment is committed to your privacy. For more information view our Privacy Statement
-
Columbus
2885 Route 206 South, Bldg. 4
Columbus, NJ 08022
(609) 288-6637
Get Directions
-
Elmer
670 Route 40
Elmer, NJ 08318
(856) 358-2880
Get Directions
-
Marlboro
65 State Route 34 unit 1
Marlboro, NJ 07746
(732) 938-6677
Get Directions
-
Hammonton
100 US Route 206
Hammonton, NJ 08037
(609) 704-9440
Get Directions
-
Columbia
228 Route 94
Columbia, NJ 07832
(908) 362-6916
Get Directions
Copyright © 2017 - 2025 Site by EquipmentLocator.com AM